injection en plastique
injection plastique
Le moulage par injection plastique est un processus de fabrication essentiel pour la production de pièces en plastique complexes et de haute qualité. En tant qu’ingénieur de conception, comprendre ce processus peut considérablement améliorer vos conceptions et optimiser la fabrication. Ce guide a pour but de vous fournir une compréhension complète du moulage par injection plastique afin de vous aider à concevoir des pièces plus efficaces et à éviter les erreurs courantes.
TABLE DES MATIERES
injection plastique
Qu’est ce que le moulage par injection plastique ?
Le moulage par injection plastique est un procédé de fabrication qui consiste à injecter du plastique fondu dans un moule pour créer une pièce. Une fois refroidie et solidifiée, la pièce est éjectée du moule, prête à être utilisée ou assemblée.
Quels sont les avantages de l’injection plastique ?
L’injection plastique permet de réaliser des composants techniques et d’aspect de formes complexes à des couts très bas. Les produits de grande consommation ont généralement recours à cette technologie de moulage de thermoplastiques pour apporter des fonctions de capotage, boutons ou autres fonctions d’aspect.
Quels sont les inconvénients du moulage par injection plastique ?
Le moulage par injection plastique est un procédé de fabrication qui consiste à injecter du plastique fondu dans un moule pour créer une pièce. Une fois refroidie et solidifiée, la pièce est éjectée du moule, prête à être utilisée ou assemblée.
Les étapes d’un projet en injection plastique
Conception pièce plastique
La première étape consiste à concevoir la pièce en utilisant des logiciels de CAO (conception assistée par ordinateur). Il est crucial de prendre en compte les spécificités du moulage par injection dès cette phase pour éviter des modifications coûteuses par la suite.
La deuxième étape du processus consiste à créer le moule en fonction de la conception de la pièce. Cette phase est cruciale car la qualité du moule affectera directement la qualité de la pièce finale. Les moules sont généralement fabriqués en acier ou en aluminium et sont conçus pour résister aux hautes températures et pressions du processus de moulage. Il est essentiel de collaborer étroitement avec les fabricants de moules pour s’assurer que toutes les spécifications sont respectées et que le moule sera à la fois durable et efficace.
moules pour injection plastique
Types de Moules pour Injection Plastique
Il existe plusieurs types de moules utilisés dans le moulage par injection plastique, chacun conçu pour répondre à des besoins spécifiques en termes de production, de coût et de complexité.
moules injection petite série
Moule d’injection prototype
Caractéristiques des Moules pour Prototypes
Coût Réduit:
Les moules prototypes peuvent être réalisés en impression 3D, en usinage CNC dans de l’acier ou de l’aluminium.
Les moules de prototypes sont souvent fabriqués dans des matériaux moins coûteux comme l’aluminium, ce qui réduit les dépenses initiales. Cela est particulièrement avantageux lorsque multiples itérations de conception sont nécessaires.
Temps de Fabrication Court:
Grâce à des processus de fabrication simplifiés et des matériaux plus faciles à travailler, les moules de prototypes peuvent être produits plus rapidement que les moules pour la production en série. Cela permet d’accélérer le cycle de développement et d’introduire les produits sur le marché plus rapidement.
Flexibilité et Adaptabilité:
Les moules pour prototypes peuvent être modifiés plus facilement que les moules de production en série. Cette flexibilité permet aux ingénieurs de conception d’expérimenter différentes configurations et d’optimiser la conception avant de valider le moule final.
Il existe plusieurs types de moules utilisés dans le moulage par injection plastique, chacun conçu pour répondre à des besoins spécifiques en termes de production, de coût et de complexité.
moules injection moyenne série
Moule d’injection plastique mono empreinte
Ce type de moule est conçu pour produire une pièce à la fois. Ils sont généralement utilisés pour les petites séries de production ou les pièces de grande taille. Les moules à cavité unique sont simples à fabriquer et moins coûteux, mais ils ne sont pas idéaux pour les hauts volumes de production.
Moules à Canaux Froids :
Contrairement aux moules à canaux chauds, les moules à canaux froids permettent au plastique dans les canaux de se solidifier entre les cycles de moulage. Ils sont moins chers à fabriquer mais peuvent générer davantage de déchets de plastique, nécessitant une gestion supplémentaire des matériaux.
Inconvénients des Moules à Canaux Froids
Augmentation des Déchets de Matière:
Les moules à canaux froids génèrent plus de déchets car le plastique dans les canaux se solidifie entre les cycles de moulage. Ce surplus doit être retiré et souvent recyclé, ce qui ajoute des étapes supplémentaires au processus de production.
Efficacité de Production Réduite :
Comparé aux moules à canaux chauds, les moules à canaux froids sont moins efficaces pour les grandes séries de production. Le temps nécessaire pour que le plastique redevienne fondu et prêt à être injecté peut ralentir considérablement le rythme de fabrication.
Charges Thermiques Inégales :
Avec les canaux froids, il y a une distribution inégale de la chaleur à l’intérieur du moule, ce qui peut entraîner des défauts de moulage comme des marques de brûlure, des lignes de soudure et des variations dimensionnelles dans les pièces produites.
Maintenance et Usure du Moule :
Les cycles thermiques intenses associés à la transition constante entre le plastique fondu et solidifié dans les canaux peuvent accélérer l’usure du moule. Cela entraîne des coûts de maintenance plus élevés et une durabilité réduite du moule.
Gestion Complexe des Déchets :
La nécessité de retirer et de recycler ou d’éliminer les déchets de matière ajoute des contraintes logistiques. Ceci non seulement augmente les coûts, mais aussi la complexité de la gestion des matières résiduelles dans l’environnement de production.
Bien que les moules à canaux froids puissent représenter une option plus économique lors de la fabrication initiale, leurs inconvénients en termes de déchets, de durée de cycle, de défauts de pièces, et de maintenance en font une solution moins viable pour les grandes séries de production. Les ingénieurs doivent donc soigneusement évaluer les besoins de leurs projets avant de choisir le type de moule le plus adapté.
moules injection grande série
Moule d’injection multi empreintes
Les moules à cavités multiples peuvent produire plusieurs pièces en une seule fois, ce qui augmente considérablement la cadence de production. Ils sont parfaits pour les grandes séries de production. Cependant, leur conception et fabrication sont plus complexes et coûteuses.
Moules à bloc chaud
Ces moules utilisent des chauffages internes pour maintenir le plastique fondu à une température optimale, ce qui réduit le gaspillage de matière et améliore la qualité des pièces. Les moules à canaux chauds sont particulièrement bénéfiques pour les grandes séries de production, bien que leur coût initial soit plus élevé.
Blocs Chauds à Injection Séquentielle
Avantages des Blocs Chauds à Injection Séquentielle
Les blocs chauds à injection séquentielle représentent une avancée technologique significative dans le domaine du moulage par injection plastique. Ce système permet d’injecter le plastique fondu dans le moule par étapes séquentielles plutôt qu’en une seule fois.
Contrôle Amélioré du Flux de Matière :
En permettant une injection séquentielle, le flux de matière est plus contrôlé, réduisant ainsi les risques de défauts potentiels comme les lignes de soudure ou les inclusions.
Réduction des Contraintes Internes :
Le moulage séquentiel diminue les contraintes internes dans la pièce moulée, améliorant ainsi ses propriétés mécaniques et sa durabilité.
Qualité Esthétique Supérieure :
Ce procédé permet une finition de surface plus homogène et esthétique grâce à une meilleure gestion de la pression et de la température dans les différentes zones du moule.
Optimisation de la Répartition de la Matière :
Grâce à une meilleure répartition de la matière, le poids de la pièce peut être optimisé, contribuant à une réduction des coûts de production.
Applications Courantes
Les blocs chauds à injection séquentielle sont souvent utilisés dans la fabrication de pièces complexes et de grandes dimensions, où la qualité et la précision sont primordiales. Ils sont particulièrement répandus dans l’industrie automobile, l’aérospatiale et pour les pièces techniques nécessitant une haute performance.
La mise en œuvre de blocs chauds à injection séquentielle nécessite une collaboration étroite entre les ingénieurs de conception et les fabricants de moules pour s’assurer que le système répond de manière optimale aux exigences spécifiques du projet.
TECHNOLOGIES DE MOULES POUR L’inJECTION PLASTIQUE
MOULE PLASTIQUE INJECTION
Moules à Éjection Automatique :
Il existe plusieurs types de moules utilisés dans le moulage par injection plastique, chacun conçu pour répondre à des besoins spécifiques en termes de production, de coût et de complexité.
La majorité des moules sont équipés de mécanismes pour éjecter automatiquement les pièces après leur formation, ce qui améliore l’efficacité du processus. Ils sont idéaux pour les productions à grande échelle où la rapidité et la répétabilité sont essentielles. A contrario, les moules d’injection plastique prototype peuvent être réalisés sans système d’éjection. La pièce est donc démoulée à la main.
Moules à Tiroirs
Les moules à tiroirs sont des outils complexes conçus pour fabriquer des pièces présentant des formes ou des caractéristiques qui ne peuvent pas être simplement éjectées d’un moule conventionnel. Ils possèdent des éléments mobiles, appelés tiroirs ou mouvements latéraux, qui se rétractent ou se déplacent latéralement pour libérer les parties de la pièce comportant des contre-dépouilles ou d’autres géométries complexes. Ces tiroirs sont actionnés mécaniquement, souvent par des dispositifs tels que des cabestans ou des broches, ou hydrauliquement.
Ce type de moule est particulièrement avantageux pour la production de pièces à géométries difficiles, comme des trous latéraux, des filets intérieurs ou des formes sous-détentes. Bien que leur conception et fabrication soient plus coûteuses et techniques, les moules à tiroirs permettent de produire des pièces qui seraient impossibles ou beaucoup plus coûteuses à usiner par d’autres procédés.
La flexibilité offerte par ces moules en fait un choix stratégique pour les ingénieurs de conception souhaitant repousser les limites de la complexité des pièces en plastique.
Moules à Dévissage
Les moules à dévissage sont spécifiquement conçus pour produire des pièces comportant des filets internes ou externes, comme des bouchons de bouteilles ou des composants à vis. Contrairement aux moules traditionnels où les pièces sont simplement éjectées, les moules à dévissage intègrent un mécanisme de filetage qui permet aux pièces de se dévisser du noyau du moule avant d’être éjectées.
Ce procédé est réalisé grâce à des broches rotatives motorisées ou à des dispositifs mécaniques tels que des crémaillères et des pignons, actionnés par des mouvements de la machine de moulage ou par des servo-moteurs. Les moules à dévissage offrent plusieurs avantages, notamment la possibilité de produire des filets précis et de haute qualité, ainsi que la réduction du besoin de post-traitement ou d’usinage secondaire.
Bien que la conception et la fabrication de moules à dévissage soient plus complexes et onéreuses, ils sont indispensables pour de nombreuses applications industrielles où des fixations filetées sont nécessaires. En collaborant étroitement avec les fabricants de moules et en tenant compte des spécificités de la pièce dès la phase de conception, il est possible d’optimiser le processus de moulage pour obtenir des pièces filetées fonctionnelles et esthétiques.
En choisissant le bon type de moule pour votre projet, vous pouvez optimiser votre processus de production, améliorer la qualité des pièces produites et réduire les coûts globaux.
Démoulage par Cales Montantes
Le démoulage par cales montantes est une technique spécialisée utilisée pour extraire des pièces moulées comportant des caractéristiques géométriques complexes, telles que des sous-dépouilles profondes ou des structures en porte-à-faux. Cette méthode implique l’utilisation de cales inclinées qui se déplacent verticalement ou horizontalement pendant le processus de démoulage, permettant ainsi de libérer délicatement la pièce du moule sans endommager ses détails ou provoquer des déformations.
Les cales montantes sont généralement actionnées par des mécanismes tels que des pistons hydrauliques ou pneumatiques, ou par des systèmes mécaniques intégrés à la machine de moulage. Lors de la phase d’ouverture du moule, les cales se rétractent ou se déplacent à un angle précis pour dégager les zones de la pièce qui sont difficiles à éjecter par des méthodes traditionnelles. Cela assure une extraction propre et efficace de la pièce, minimisant ainsi les risques de déformation ou de défauts de surface.
L’utilisation de cales montantes est particulièrement bénéfique lors de la production de pièces complexes en plastique qui nécessitent une finition soignée et précise. Toutefois, il est important de noter que la conception et la fabrication de moules intégrant des cales montantes sont plus complexes et coûteuses. Une collaboration étroite avec les concepteurs de moules est essentielle pour s’assurer que tous les aspects du mécanisme de démoulage sont bien intégrés et optimisés.
En résumé, le démoulage par cales montantes offre une solution efficace pour la production de pièces plastiques complexes, tout en maintenant une haute qualité et une intégrité dimensionnelle.
durée de vie des moules d’injection plastique
Durée de vie et construction des moules
La durée de vie et la construction des moules sont des facteurs déterminants pour le succès de toute opération de moulage par injection. La Society of Plastics Engineers (SPE) a établi des classifications spécifiques pour les moules, connues sous le nom de « Classes SPE », afin de standardiser et d’optimiser ce processus. Ces classes déterminent les matériaux, les techniques de fabrication, et la durabilité escomptée des moules en fonction des besoins de production.
Classe 101 : Cette classe représente les moules pour des productions à très haut volume, souvent dépassant un million de cycles. Ces moules sont fabriqués à partir de matériaux de haute qualité et d’aciers alliés et subissent des traitements thermiques pour assurer une excellente durabilité. Ils sont conçus pour une utilisation intensive et continue, souvent équipés de systèmes de refroidissement sophistiqués pour maintenir la productivité.
Classe 102 : Les moules de cette classe sont destinés à des productions de volume élevé, entre 500 000 et 1 000 000 de cycles. Comme la Classe 101, ils sont fabriqués à partir de matériaux durables, mais peuvent tolérer des niveaux de production légèrement inférieurs. Ils conviennent aux environnements de production où la qualité élevée et la longévité sont nécessaires, mais où les exigences de volume ne justifient pas les coûts supplémentaires de la Classe 101.
Classe 103 : Représentant les moules pour des productions moyennes, allant de 100 000 à 500 000 cycles, les moules de Classe 103 sont souvent utilisés pour des produits de consommation ou pour des pièces nécessitant des ajustements fréquents de conception. La sélection des matériaux et la construction de ces moules sont moins coûteuses, tout en offrant une qualité suffisante pour des productions mi-longues.
Classe 104 : Idéale pour des volumes de production inférieurs, entre 10 000 et 100 000 cycles, la Classe 104 est généralement utilisée pour les prototypes ou les séries limitées. Les matériaux utilisés pour ces moules sont plus économiques et la construction est simplifiée, rendant cette classe adaptée pour les tests de marché ou les validations de nouvelles conceptions.
Classe 105 : Ces moules sont spécifiés pour des productions très basses, jusqu’à 10 000 cycles. Fabriqués à partir de matériaux moins résistants, ils sont parfaits pour des prototypes initiaux ou des productions expérimentales où les coûts de fabrication doivent être minimisés.
En comprenant ces classes et en travaillant étroitement avec les fabricants de moules, on peut sélectionner le type de moule approprié pour chaque projet, assurant ainsi un équilibre optimal entre coûts, durabilité et qualité de production.
PRIX d’un moule d’injection plastique ?
Comprendre les Coûts d’un Moule d’Injection
Le coût d’un moule d’injection varie considérablement en fonction d’un certain nombre de facteurs spécifiques. Parmi eux, on trouve la complexité de la pièce à produire, les matériaux utilisés pour la fabrication du moule, et les exigences de production. Il est essentiel de comprendre ces coûts pour prendre des décisions éclairées et optimiser les budgets de production.
Complexité de la Conception:
Plus la conception de la pièce est complexe, plus le moule sera coûteux. Les fonctionnalités comme les formes sous-cavitées, les courbes complexes ou les nuances précises nécessitent des techniques de fabrication avancées et un temps de main-d’œuvre accru.
Type de Matériaux:
Les matériaux utilisés pour construire les moules varient en fonction de la classe et des exigences de durabilité. Les moules de Classe 101, par exemple, utilisent des aciers de haute qualité traités thermiquement, tandis que les moules de Classe 105 peuvent être fabriqués en aluminium ou d’autres matériaux moins coûteux.
Volume de Production:
Les exigences en termes de volume de production impactent également le coût. Un moule destiné à une production de millions de pièces sera plus robuste et plus cher à fabriquer que celui conçu pour une série limitée ou des prototypes.
Technologies de Fabrication:
L’utilisation de technologies avancées comme l’usinage à commande numérique (CNC), la texturation laser, ou l’impression 3D dans la fabrication du moule peut augmenter le coût initial, mais offre des avantages en termes de précision et de qualité.
Coûts de Maintenance et Réparations:
Un autre facteur à considérer est le coût de maintenance et de réparations sur la durée de vie du moule. Les moules de classe supérieure nécessitent des interventions moins fréquentes, mais leur entretien peut être plus coûteux en raison des matériaux haut de gamme utilisés.
Comprendre ces différents aspects permet aux fabricants de choisir le moule le mieux adapté à leurs besoins budgétaires et de production. Ainsi, ils peuvent garantir une production efficace et rentable, tout en maintenant une qualité optimale des pièces fabriquées.
Ainsi, les moules pour injection de prototypes sont un outil indispensable dans le développement efficace et économique de nouveaux produits en plastique.
délai de fabrication d’un moule d’injection plastique ?
Quel est le délai de fabrication d’un moule d’injection ?
Le délai de fabrication d’un moule d’injection dépend d’un certain nombre de facteurs, parmi lesquels la complexité de la pièce, les matériaux utilisés et la charge de travail actuelle du fabricant de moules.
En général, pour un moule de production standard, le temps de fabrication peut varier de 8 à 16 semaines. Toutefois, ce délai peut être raccourci pour des moules de prototypes ou allongé pour des moules particulièrement complexes. Des processus supplémentaires tels que la texturation, le traitement thermique ou l’assemblage de composants multiples peuvent également influencer le délai final.
Il est essentiel de planifier intelligemment et de travailler en étroite collaboration avec le fabricant pour s’assurer que les délais sont respectés et alignés avec le calendrier de lancement de produit.
Avec une bonne planification et une communication efficace, les délais de fabrication peuvent être optimisés pour garantir un processus de développement fluide et rapide. En fin de compte, un moule d’injection bien conçu et bien fabriqué est la clé d’une production en série réussie et rentable.
fabrication de moule en chine
Moules d’injection Chine
La Chine s’est imposée comme un acteur majeur dans la fabrication de moules d’injection, offrant une combinaison de coûts compétitifs, de savoir-faire technique et de capacités de production élevées. Grâce à une main-d’œuvre qualifiée et à des technologies de pointe, les fabricants chinois peuvent produire des moules de haute qualité adaptés aux besoins variés des clients internationaux.
Avantages de la Fabrication de Moules en Chine ?
Coût Réduit:
Le coût de la main-d’œuvre en Chine est généralement inférieur à celui des pays occidentaux. Cela se traduit par une réduction significative des coûts de production, rendant la fabrication de moules plus économique.
Technologie et Innovation:
Les fabricants chinois investissent continuellement dans des technologies avancées telles que l’usinage à grande vitesse, la texturation laser et l’impression 3D. Ces innovations permettent d’améliorer la précision et la qualité des moules produits.
Capacités de Production:
La Chine dispose d’une capacité de production impressionnante et peut gérer des commandes de grande envergure. Qu’il s’agisse de prototypes ou de moules de production en série, les fabricants chinois peuvent répondre rapidement aux demandes des clients.
Expérience et Expertise:
Avec des décennies d’expérience dans la fabrication de moules, les fabricants chinois ont développé une expertise approfondie. Ils sont capables de conseiller et de collaborer étroitement avec les clients pour optimiser la conception et la fonctionnalité des moules.
Défis et Considérations pour la fabrication de moules d’injection en chine ?
Normes de Qualité:
La qualité des moules peut varier d’un fabricant à l’autre. Il est crucial de choisir des fabricants ayant de bonnes références et des certifications internationales reconnues pour garantir des normes de production élevées.
Communication:
Les barrières linguistiques et les différences culturelles peuvent parfois compliquer la communication. Travailler avec des agents intermédiaires ou des consultants locaux peut aider à surmonter ces obstacles.
Logistique et Délais:
La logistique internationale peut présenter des défis, notamment en ce qui concerne les délais de transport et les formalités douanières. Une planification méticuleuse est nécessaire pour assurer une chaîne d’approvisionnement fluide.
Propriété Intellectuelle:
La protection de la propriété intellectuelle est une préoccupation majeure lorsqu’on travaille avec des fabricants étrangers. Il est essentiel d’établir des accords de confidentialité solides et de consulter des conseils juridiques pour protéger les conceptions et les innovations.
Conclusion
La fabrication de moules en Chine offre de nombreux avantages, notamment des coûts réduits et des capacités de production élevées, tout en comportant des défis qui nécessitent une gestion rigoureuse. En collaborant avec des partenaires fiables et en prenant des mesures proactives pour surmonter les obstacles potentiels, les entreprises peuvent tirer pleinement parti des opportunités offertes par la Chine dans le domaine de la fabrication de moules d’injection.
fabrication de moule en france
fabrication de moule au portugal
fabrication de moule en italie
Fabrication de Moules en France et en Europe
La fabrication de moules en France et en Europe occupe une place importante grâce à un héritage établi de précision et de qualité. Des pays comme l’Allemagne, la Suisse et l’Italie sont également réputés pour leur savoir-faire exceptionnel dans la conception et la fabrication de moules. Ces régions offrent plusieurs avantages distincts qui peuvent séduire les entreprises cherchant à équilibrer la qualité, la communication et les délais de livraison.
Avantages de la Fabrication de Moules en France et en Europe
Haute Qualité :
Les fabricants européens sont réputés pour produire des moules de très haute qualité. Grâce à des normes de fabrication strictes et des certifications reconnues, les moules produits en Europe sont synonyme de précision et de durabilité.
Proximité Géographique :
Pour les entreprises basées en Europe, choisir un fabricant local peut réduire considérablement les délais de livraison et faciliter les visites sur place pour un suivi plus rigoureux du projet.
Communication Facile :
Travailler avec des fabricants européens peut réduire les barrières linguistiques et culturelles, améliorant ainsi la compréhension mutuelle et la collaboration.
Innovation et Technologie :
Les fabricants européens investissent continuellement dans les technologies de pointe. Ils sont souvent à l’avant-garde de l’innovation avec des techniques comme l’usinage à grande vitesse, la texturation laser et l’impression 3D.
Respect des Normes Environnementales :
Les pays européens ont des réglementations strictes en matière d’environnement, ce qui garantit que les processus de fabrication des moules respectent des normes écologiques élevées.
Défis et Considérations
Coûts Élevés :
Le coût de la main-d’œuvre et des matières premières en Europe est généralement plus élevé comparé à d’autres régions, ce qui peut augmenter le prix final des moules.
Disponibilité et Capacité :
La demande élevée pour des moules de qualité peut souvent entraîner des temps d’attente plus longs chez certains fabricants européens, ce qui nécessite une planification avancée.
Réglementations Complexes :
Les différents pays européens peuvent avoir des réglementations variées concernant la fabrication et l’import/export, ce qui peut compliquer la logistique et augmenter les délais.
Conclusion
La fabrication de moules en France et en Europe présente de nombreux avantages, notamment une qualité supérieure, une communication facile et des innovations technologiques avancées. Bien que les coûts puissent être plus élevés, les bénéfices en termes de précision, de durabilité et de conformité échouent souvent à compenser ces dépenses supplémentaires. En planifiant soigneusement et en travaillant avec des fabricants de confiance, les entreprises peuvent garantir que leurs projets de fabrication de moules sont réalisés avec succès et efficacement.
cycle injection plastique
fabrication de moule au portugal
fabrication de moule en italie
Quelles sont les étapes d’un cycle d’injection plastique ?
Le cycle d’injection plastique est un processus méthodique et bien structuré qui comporte plusieurs étapes clés. Chaque étape joue un rôle essentiel pour garantir la qualité et la précision des pièces produites. Voici un aperçu des principales phases d’un cycle d’injection plastique :
Fermeture du Moule :
Le cycle commence par la fermeture des deux moitiés du moule sous une pression élevée pour s’assurer qu’il est hermétiquement scellé. Cela empêche toute fuite de matière pendant l’injection.
Injection de la Matière :
La matière plastique, généralement sous forme de granulés, est chauffée jusqu’à son point de fusion dans le cylindre de la machine. Une fois fondue, elle est injectée dans la cavité du moule à travers une buse. Cette étape nécessite un contrôle précis de la pression et de la vitesse pour obtenir une distribution homogène de la matière.
Maintien sous Pression :
Une fois la cavité du moule remplie, la pression est maintenue pour compenser le retrait de la matière en refroidissant. Cette phase est cruciale pour assurer une densité uniforme de la pièce et éviter les défauts comme les bulles d’air ou les lignes de soudure.
Refroidissement :
La matière injectée doit maintenant refroidir et se solidifier. Le temps de refroidissement dépend de la taille et de la complexité de la pièce, ainsi que du type de matériau utilisé. Des canaux de refroidissement intégrés dans le moule aident à dissiper la chaleur plus efficacement.
Ouverture du Moule :
Une fois la matière suffisamment refroidie, le moule peut être ouvert. La pièce moulée est toujours dans la cavité du moule au début de cette étape.
Éjection de la Pièce :
Des broches d’éjection ou des plaques sont utilisées pour expulser la pièce finie du moule. Il est crucial de contrôler cette étape pour éviter d’endommager la pièce, surtout si elle est encore quelque peu souple.
Retrait et Inspection de la pièce:
Une fois éjectée, la pièce peut être retirée et inspectée pour vérifier sa conformité aux spécifications et détecter d’éventuels défauts. Au besoin, des ajustements peuvent être réalisés sur les paramètres de la machine ou le design du moule pour améliorer la qualité de la pièce.
La compréhension et l’optimisation de chacune de ces étapes permettent d’améliorer l’efficacité, la qualité et la rentabilité du processus d’injection plastique.
temps de cycle injection plastique
moulage plastique
injection plastique
plastique moulage
Comment calcule-t-on le temps de cycle d’un produit injecté en plastique ?
Le temps de cycle d’un produit injecté en plastique est une métrique cruciale qui influence directement la productivité et les coûts de production. Calculer ce temps avec précision permet d’optimiser le processus de moulage par injection et d’assurer une production efficace. Voici les principales étapes pour déterminer le temps de cycle :
Retrouvez notre calculateur de temps de cycle d’injection plastique en ligne
Temps d’Injection :
Cette phase correspond au temps nécessaire pour que la matière plastique fondu soit injectée dans le moule. Le temps d’injection dépend du volume de la cavité, de la vitesse d’injection, et de la viscosité du matériau.
Temps de Maintien sous Pression :
Après l’injection, la matière est maintenue sous pression pour compenser le retrait et assurer une densité uniforme de la pièce. Le temps de maintien est généralement une fraction du temps total de cycle mais est crucial pour la qualité finale du produit.
Temps de Refroidissement :
C’est souvent la phase la plus longue du cycle. Le temps de refroidissement dépend de plusieurs facteurs, tels que la taille et l’épaisseur de la pièce, le type de matériau et l’efficacité du système de refroidissement intégré au moule.
Temps d’Ouverture et d’Éjection :
Une fois que la matière plastique a suffisamment refroidi, le moule s’ouvre et la pièce est éjectée. Le temps d’ouverture et d’éjection est généralement constant mais doit être pris en compte pour une estimation précise du temps de cycle.
Temps Additionnels :
Il peut y avoir d’autres délais mineurs, comme le temps de retrait de la pièce, l’inspection post-éjection et le temps nécessaire pour réinitialiser le moule pour le prochain cycle.
Le temps de cycle total est la somme de tous ces temps. Ainsi, pour optimiser la production, il est essentiel de minimiser le temps de chaque phase sans compromettre la qualité de la pièce produite. Des technologies avancées et des systèmes de refroidissement performants peuvent considérablement réduire le temps de cycle, augmentant ainsi l’efficacité et la rentabilité du processus de moulage par injection.
matières platiques
matières thermoplastiques
élastomères
Matériaux Utilisés dans le Moulage par Injection Plastique
Polypropylène (PP)
Qu’est-ce que le Polypropylène ?
Le polypropylène (PP) est un polymère thermoplastique couramment utilisé dans un large éventail d’applications. Il se distingue par sa robustesse, sa capacité à être moulé à chaud, et sa résistance aux produits chimiques et à l’usure. Le polypropylène est également léger, ce qui le rend utile dans des applications où le poids est un facteur déterminant. Sa capacité à être recyclé ajoute à sa popularité dans les industries soucieuses de l’environnement.
Applications du Polypropylène
Emballages:
Le polypropylène est fréquemment utilisé pour fabriquer des emballages alimentaires, tels que les contenants réutilisables, les films plastiques, et les bouchons de bouteilles. Sa résistance aux acides et à l’alcool le rend idéal pour cette utilisation.
Produits Médicaux:
En raison de ses propriétés stérilisables et non-toxiques, le polypropylène est largement utilisé dans l’industrie médicale pour des produits comme les seringues, les récipients pour médicaments, et les équipements de laboratoire.
Automobile:
Ce matériau est également utilisé dans l’industrie automobile pour fabriquer des pièces légères mais durables telles que les pare-chocs, les tableaux de bord, et les réservoirs de carburant.
Textiles:
Le polypropylène est fréquemment utilisé dans la production de fibres et de textiles, incluant les sacs en polypropylène, les tapis, et les matériaux de géotextiles.
Électronique:
En raison de sa bonne isolation électrique, le polypropylène est utilisé dans les composantes électroniques telles que les condensateurs et les boîtiers de câblage.
Le polypropylène, grâce à ses diverses propriétés, continue de jouer un rôle essentiel dans de nombreuses industries, offrant des solutions efficaces et durables.
Polyéthylène (PE)
Qu’est-ce que le Polyéthylène ?
Le polyéthylène (PE) est un polymère thermoplastique largement utilisé, reconnu pour sa simplicité de production et son coût relativement bas. Il est constitué de longues chaînes d’éthylène et se présente sous plusieurs formes en fonction de la densité et de la ramification des chaînes polymères, notamment le polyéthylène basse densité (PEBD), le polyéthylène haute densité (PEHD), et le polyéthylène linear basse densité (PELLD). Chacune de ces formes possède des propriétés spécifiques qui les rendent adaptées à diverses utilisations.
Applications du Polyéthylène
Emballages:
Le polyéthylène est très utilisé dans l’industrie de l’emballage, notamment pour la fabrication de films plastiques, de sacs, et de bouteilles. Le PEBD est particulièrement apprécié pour les sacs en plastique en raison de sa flexibilité et de sa résistance à la déchirure.
Construction:
En construction, le PEHD est souvent utilisé pour les conduites d’eau et de gaz, les géomembranes, et les plastiques de protection. Sa robustesse et sa résistance chimique le rendent idéal pour ces applications.
Produits de Consommation:
Le polyéthylène est couramment utilisé dans la fabrication de divers produits de consommation, tels que les jouets, les ustensiles de cuisine, et les équipements de sport. Sa légèreté et sa malléabilité sont des atouts majeurs.
Agriculture:
Dans l’agriculture, les films de polyéthylène sont utilisés pour les serres et les tunnels de culture, contribuant ainsi à la protection des plantes et à l’amélioration des rendements. Le PEBD est préféré pour ces usages en raison de sa transparence et de sa capacité à filtrer les rayons UV.
Santé et Médical:
Le polyéthylène trouve également des applications dans le secteur médical pour la fabrication de gants jetables, de tubulures et de diverses fournitures de laboratoire. Son inertie chimique et sa biocompatibilité en font un choix idéal pour ces produits.
Le polyéthylène, grâce à sa polyvalence et à ses propriétés avantageuses, est un matériau essentiel dans de nombreux secteurs industriels, offrant des solutions fiables et économiques.
Polystyrène (PS)
Qu’est-ce que le Polystyrène ?
Le polystyrène (PS) est un polymère synthétique thermoplastique largement utilisé dans diverses applications industrielles et commerciales. Ce matériau se distingue par sa rigidité, sa transparence et sa facilité de moulage, ce qui le rend particulièrement adapté pour des produits nécessitant une haute précision et des détails précis. Le polystyrène existe sous deux formes principales : le polystyrène expansé (PSE) et le polystyrène extrudé (XPS).
Applications du Polystyrène
Le polystyrène expansé est couramment utilisé pour les emballages de protection, comme les housses pour appareils électroniques, et les produits alimentaires, tels que les gobelets et les barquettes. Sa légèreté et ses excellentes propriétés d’isolation thermique en font également un choix populaire dans le secteur de la construction pour l’isolation des murs, des toits et des planchers.
Le polystyrène extrudé, quant à lui, est souvent employé pour des applications nécessitant une plus grande durabilité et rigidité. On le retrouve dans les panneaux isolants, les modèles réduits, et différents types de produits durables, tels que les gadgets électroniques et les pièces automobiles.
En résumé, grâce à sa polyvalence, sa durabilité et son coût relativement bas, le polystyrène continue d’être un choix de premier plan dans de nombreux secteurs industriels, allant de l’emballage à la construction en passant par les produits de consommation.
Chaque matériau a ses propres caractéristiques qui influencent le choix en fonction des exigences de la pièce (résistance, flexibilité, coût, etc.).
Polycarbonate (PC)
Qu’est ce que le polycarbonate ?
Le polycarbonate (PC) est un polymère thermoplastique connu pour sa robustesse exceptionnelle, sa transparence et sa résistance aux températures élevées. Ces propriétés le rendent particulièrement précieux dans une vaste gamme d’applications où la durabilité et la clarté optique sont essentielles.
Le polycarbonate surpasse de nombreux autres plastiques en termes de résistance aux chocs, tout en maintenant une haute clarté, ce qui le rend idéal pour les usages où la transparence et la sécurité sont primordiales.
Quelles sont les applications du Polycarbonate (PC)
Les applications du polycarbonate sont variées. Dans l’industrie automobile, il est souvent utilisé pour fabriquer des phares et des vitrages qui doivent résister aux impacts et aux intempéries. En électronique, le polycarbonate est employé pour les boîtiers de divers appareils, offrant non seulement une protection robuste mais aussi une esthétique soignée. On le retrouve également dans la fabrication des CD et DVD, en raison de sa grande stabilité dimensionnelle et de sa capacité à maintenir une qualité d’image et de son élevée.
Dans le domaine de la construction, le polycarbonate est couramment utilisé pour les vitrages et les toitures translucides, grâce à ses excellentes propriétés d’isolation thermique et de transmission de lumière. Dans les équipements de protection individuelle, tels que les lunettes de sécurité et les casques, le polycarbonate offre une protection fiable contre les chocs et les éclats.
En résumé, le polycarbonate est un matériau incontournable dans de nombreux secteurs grâce à ses propriétés mécaniques et optiques exceptionnelles. Sa polyvalence et sa durabilité en font un choix préféré pour des applications nécessitant des performances élevées et une sécurité accrue.
Acrylonitrile Butadiène Styrène (ABS)
Qu’est ce que l’ABS ?
L’Acrylonitrile Butadiène Styrène (ABS) est un polymère thermoplastique couramment utilisé en raison de ses excellentes propriétés mécaniques et son coût abordable.
L’ABS est composé d’acrylonitrile, de butadiène et de styrène, qui contribuent chacun à ses caractéristiques spécifiques :
- l’acrylonitrile offre une résistance chimique et thermique,
- le butadiène donne de la ténacité et de la résistance aux chocs, tandis que
- le styrène procure une rigidité et une facilité de façonnage.
Cette combinaison fait de l’ABS un matériau robuste et polyvalent.
Applications de l’ABS
Automobile:
L’ABS est fréquemment utilisé dans l’industrie automobile pour la fabrication de divers composants, tels que les tableaux de bord, les pare-chocs, les panneaux de carrosserie et les grilles de radiateur. Sa résistance aux chocs et sa capacité à être moulé en formes complexes en font un matériau idéal pour ces applications.
Électronique:
En électronique, l’ABS est utilisé pour les boîtiers de produits tels que les ordinateurs, les téléphones portables, et les écrans de télévision. Ses propriétés isolantes et sa résistance aux impacts protègent les composants électroniques délicats à l’intérieur de ces appareils.
Électroménagers:
Les appareils électroménagers comme les réfrigérateurs, les aspirateurs, et les lave-linge bénéficient également des avantages de l’ABS. Ce matériau permet la fabrication de pièces aux formes complexes, offre une bonne robustesse et résiste bien à une utilisation intensive.
Jouets:
L’ABS est largement utilisé dans la fabrication de jouets, notamment les célèbres briques LEGO. La rigidité, la durabilité et la sécurité (car non toxique) de l’ABS en font le choix parfait pour les jouets qui doivent résister à une manipulation fréquente.
Impression 3D:
Dans le domaine de l’impression 3D, l’ABS est l’un des matériaux les plus utilisés. Il est apprécié pour sa capacité à être facilement extrudé et pour les pièces finales qui présentent une bonne résistance mécanique. Les objets imprimés en 3D avec de l’ABS peuvent être poncés, collés et peints, offrant ainsi une grande polyvalence pour les projets de prototypage ou de fabrication de pièces finales.
L’ABS, grâce à son équilibre unique entre coût, performance et facilité de traitement, continue d’être un matériau de choix dans diverses industries, fournissant des solutions innovantes et durables.
Chaque matériau a ses propres caractéristiques qui influencent le choix en fonction des exigences de la pièce (résistance, flexibilité, coût, etc.).
TOUTES LES FICHES TECHNIQUES DES MATIERES PLASTIQUES SONT DISPONIBLES SUR NOTRE SITE
recyclage plastique
recyclage des plastiques
plastique recyclé
Classes de recyclage des matières plastiques
Les matières plastiques sont classées en différentes catégories de recyclage pour faciliter leur tri et leur traitement dans les installations de recyclage. Chaque catégorie est identifiée par un code numérique, souvent accompagné d’un sigle, qui permet de reconnaître facilement de quel type de plastique il s’agit. Voici les principales classes de recyclage des matières plastiques :
PET (Polyéthylène Téréphtalate) – Code 1:
Utilisé principalement pour les bouteilles de boissons gazeuses et d’eau, les contenants alimentaires et certaines fibres textiles. Le PET peut être recyclé en nouveaux contenants, fibres pour vêtements et tapis.
PEHD (Polyéthylène Haute Densité) – Code 2:
Comprend les bouteilles de lait, les flacons de shampoing, et les contenants de produits ménagers. Le PEHD recyclé est couramment utilisé pour fabriquer des tuyaux, des bacs de recyclage et des plastiques de protection.
PVC (Polychlorure de Vinyle) – Code 3:
Trouvé dans les tuyaux de plomberie, les cadres de fenêtres et les cartes en plastique. Le PVC est difficile à recycler en raison de sa composition chimique, mais il peut être réutilisé dans certains produits de construction.
PEBD (Polyéthylène Basse Densité) – Code 4:
Utilisé pour les sacs en plastique, les films étirables et certains types de bouteilles. Le PEBD recyclé peut être transformé en sacs poubelles, films agricoles et matériaux de construction.
PP (Polypropylène) – Code 5:
Se trouve dans les contenants alimentaires, les bouchons de bouteilles et les pailles en plastique. Le PP recyclé est utilisé pour fabriquer des pièces automobiles, des boîtiers de batterie et des équipements de laboratoire.
PS (Polystyrène) – Code 6:
Utilisé dans les gobelets jetables, les emballages de restauration rapide et les produits de calage. Le PS est souvent recyclé en isolants, cadres de tableaux et autres produits de construction.
Autres – Code 7:
Cette catégorie regroupe les plastiques qui ne sont pas couverts par les autres codes, comme le polycarbonate et les bioplastiques. Les possibilités de recyclage varient considérablement selon le type de plastique.
Le tri et le recyclage des matières plastiques permettent de réduire les déchets plastiques dans les décharges et d’économiser des ressources en créant de nouveaux produits à partir de matériaux récupérés.
conception pièces plastique
bureau d’études plasturgie
régles de conception plasturgie
Conseils de Conception pour le Moulage par Injection
Épaisseur des Parois :
Maintenez une épaisseur de paroi uniforme pour éviter les défauts tels que le gauchissement. Des parois trop épaisses peuvent augmenter le temps de refroidissement et les coûts.
Quelles sont les épaisseurs minimum et maximum d’une pièce plastique ?
La détermination de l’épaisseur d’une pièce plastique est cruciale pour garantir sa fonctionnalité, sa résistance et son coût de production. L’épaisseur minimum d’une pièce plastique varie généralement entre 0,5 mm et 1,5 mm.
Cette finesse permet de réduire les coûts matériels et de production tout en offrant une légèreté appréciée dans diverses applications, telles que l’électronique ou l’emballage.
À l’inverse, les pièces épaisses sont souvent nécessaires pour des applications exigeant une résistance mécanique élevée ou une durabilité accrue, comme dans l’industrie automobile ou la construction. Cependant, il est important de noter que des épaisseurs plus importantes vont entraîner des coûts de production supérieurs.
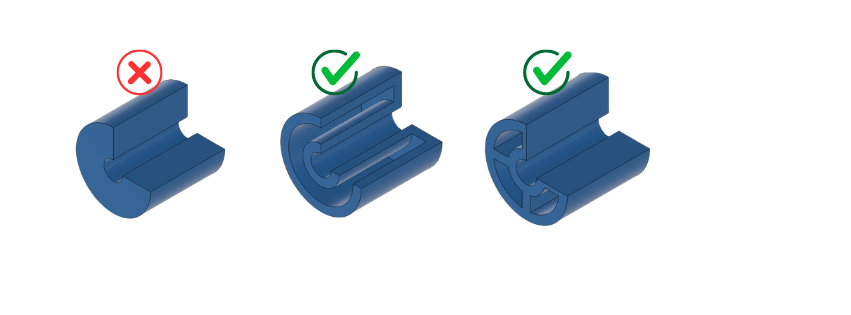
Matière | Epaisseur Mini | Epaisseur Maxi |
ABS | 1.2 | 3.5 |
POM | 0.8 | 3 |
PMMA | 0.6 | 4 |
PA | 0.8 | 3 |
PBT | 2 | 6 |
PC | 1 | 4 |
PEEK | 0.5 | 5 |
PEI | 2 | 3 |
PE | 0.8 | 5 |
PPSU | 08 | 6.5 |
PP | 1 | 4 |
PS | 0.7 | 3.2 |
TPE | 0.7 | 3.2 |
TPU | 0.7 | 3.2 |
Transitions d’épaisseur
Au dela des épaisseurs minimum et maximum appliquées au produit, il est important également de maintenir une épaisseur constante du produit autant que possible. Des variations fortes des épaisseurs de manière franche apporteront inévitablement des déformations ou des défauts de surface.
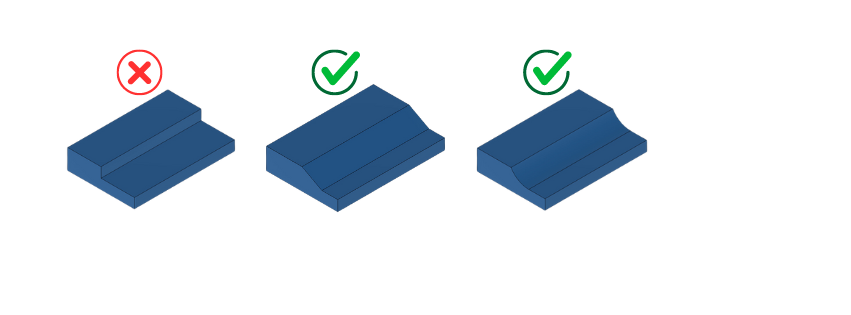
Angles de dépouille:
Ajoutez des angles de dépouille (généralement entre 1° et 2°) aux parois verticales de la pièce pour faciliter l’éjection du moule.
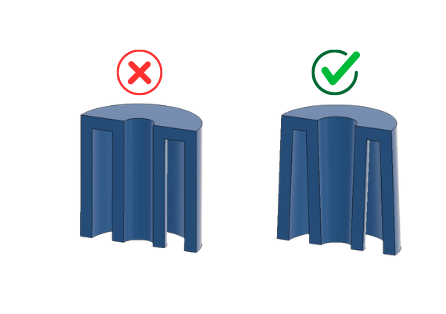
Renforts et Nervures sur pièces plastiques
Utilisez des nervures pour renforcer la structure de la pièce sans augmenter significativement l’épaisseur des parois.
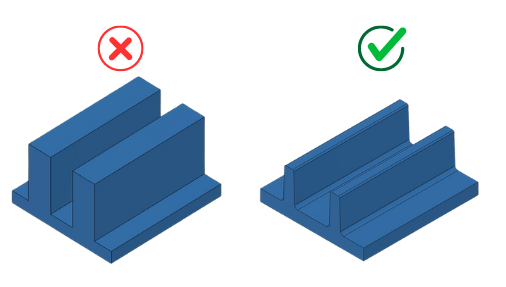
Epaisseur des nervures : 0.5 à 0,7 x L’épaisseur nominale du produit
Hauteur nervure : 2 à 3 fois l’épaisseur nominal maximum
Espacement des nervures : a minima 2 x L’épaisseur nominale de la pièce
Réduire les lignes de Soudures:
Concevez les pièces pour minimiser les lignes de soudure, qui peuvent affaiblir la structure de la pièce.
Points d’Injection:
Positionnez les points d’injection de manière que le plastique fondu remplisse le moule de manière homogène et évite les vides et les bulles d’air.
Rayons et congés
Dimensionnez les rayons de telle sorte que la pièce ait une épaisseur constante, meme dans les angles. On prend comme règle générale :
E = Epaisseur
RI = Rayon Intérieur = T
Re = Rayon extérieur = 2xT (ou T+RI)
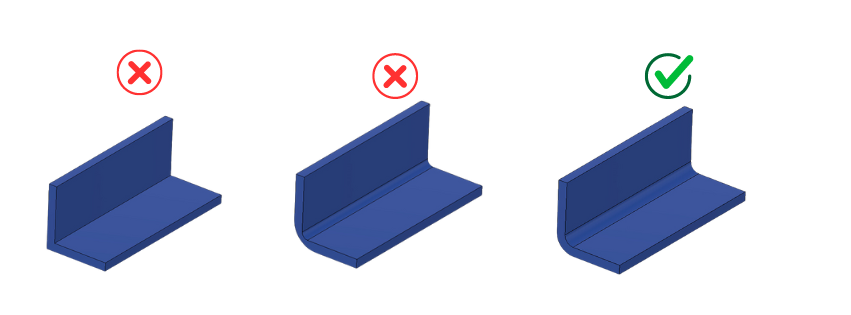
indice de réparabilité
loi agec
obsolécence programmée
Optimiser la Réparabilité (Loi Agec)
Assemblages Démontables
La conception d’assemblages démontables est fondamentale pour prolonger la durée de vie des produits et faciliter leur entretien, réparation ou recyclage.
Un assemblage démontable permet de séparer rapidement les composants individuels d’un produit sans endommager ces derniers, ce qui est en ligne avec la législation Agec (Anti-Gaspillage pour une Économie Circulaire).
Pour concevoir un assemblage démontable, il est recommandé de :
Utiliser des Fixations Standardisées :
Privilégiez les fixations standard telles que les vis, écrous et boulons, qui sont facilement accessibles et remplaçables.
dessiner correctement des futs de vissage pour l’assemblage de pieces plastiques. (hybster.com)
Éviter les Collages Permanents :
Limitez l’utilisation d’adhésifs ou soudures permanentes qui rendent le démontage difficile et peuvent endommager les composants.
Concevoir des Systèmes de Clipsage :
Intégrez des mécanismes de clipsage ou d’encliquetage qui permettent un montage et un démontage rapides et sans outils spéciaux.
Prévoir des Points d’Accès :
Assurez-vous que les points d’accès aux fixations soient facilement accessibles pour simplifier les opérations de démontage.
Étiquetage et documentation:
Fournir une documentation claire et des étiquetages détaillés pour guider les utilisateurs et techniciens dans les procédures de démontage et de remontage.
Optimiser la Réparabilité
L’optimisation de la réparabilité d’un produit est une étape cruciale pour respecter la loi Agec et favoriser une économie circulaire. Voici quelques pratiques pour améliorer la réparabilité :
Modularité des Composants :
Concevez les produits de manière modulaire, où les différentes sections ou composants peuvent être remplacés individuellement sans nécessiter le remplacement de l’ensemble du produit.
Disponibilité des Pièces Détachées :
Assurez la disponibilité des pièces détachées pour une durée prolongée, permettant les réparations même après plusieurs années d’utilisation.
Documentation Technique :
Mettez à disposition des manuels de réparation détaillés, incluant des schémas et instructions claires, pour guider les réparateurs dans leurs interventions.
Facilité d’Accès aux Composants Fragiles :
Identifiez les composants susceptibles de s’user ou de se briser plus fréquemment et concevez le produit de manière qu’ils soient facilement accessibles et remplaçables.
Compatible avec les Outils Standards :
Conservez la compatibilité avec les outils standards pour les opérations de démontage et remontage, évitant ainsi la nécessité d’outils spécifiques.
Tests de Durabilité :
Effectuez des tests rigoureux pour identifier les points faibles du produit et les renforcer, réduisant ainsi la fréquence des réparations nécessaires.
En épousant ces principes de conception, les entreprises peuvent non seulement respecter les exigences de la loi Agec, mais également promouvoir une culture de durabilité et de responsabilité environnementale, tout en offrant des produits plus durables et économiquement viables pour les consommateurs.
indice de réparabilité
loi agec
obsolécence programmée
Conseils pour optimiser le coût d’une pièce plastique injectée
Choix du Matériau :
Sélectionnez un matériau optimisé pour le coût tout en répondant aux exigences de performance. Par exemple, opter pour des polymères recyclés ou des matières premières avec des coûts inférieurs peut réduire considérablement les dépenses
COMMENT CHOISIR UN MATERIAU PLASTIQUE ?
Optimisation de la Conception :
Simplifiez le design de la pièce pour réduire les complexités lors du moulage. Minimiser les caractéristiques non essentielles peut diminuer le temps de fabrication et les frais associés.
Utilisation de Cavités Multiples :
Lorsque cela est possible, utilisez des moules multi-cavités pour produire plusieurs pièces dans un seul cycle de moulage. Cette approche maximise l’efficacité et réduit le coût par pièce.
Réduction de l’Épaisseur des Parois :
Réduisez l’épaisseur des parois de la pièce autant que possible sans compromettre la performance. Cette technique permet de diminuer la quantité de matériau utilisé et d’accélérer le temps de refroidissement.
Maintenance Préventive du Moule :
Assurez-vous que les moules sont régulièrement entretenus pour éviter des temps d’arrêt coûteux et prolonger leur durée de vie. Une maintenance proactive peut prévenir des défauts et améliorer la qualité des pièces produites.
Automatisation et Optimisation des Processus :
Intégrer des systèmes automatisés pour le moulage, l’inspection et l’emballage afin de réduire les coûts de main-d’œuvre et d’augmenter la constance de la production. L’optimisation des conditions de moulage via des logiciels de simulation peut également améliorer l’efficacité des cycles de production.
En appliquant ces conseils, les entreprises peuvent significativement abaisser les coûts de production tout en maintenant une haute qualité des pièces plastiques injectées.
développement durable
éco conception plastique
impact carbone plastiques
Comment améliorer l’impact carbone et le cycle de vie d’une pièce moulée en plastique ?
Améliorer l’impact carbone et le cycle de vie des pièces moulées en plastique est une priorité pour les entreprises cherchant à adopter des pratiques plus durables et responsables. Voici plusieurs stratégies qui peuvent être mises en œuvre à cet effet :
Utilisation de Matériaux Recyclés :
Incorporer des polymères recyclés dans le processus de production peut réduire la dépendance aux matières premières vierges et diminuer l’empreinte carbone. Le recours à des plastiques recyclés post-consommation ou post-industriels offre une seconde vie aux matériaux et prévient l’accumulation des déchets plastiques.
LIRE l’ARTICLE SUR l’INTEGRATION DE MATIERES RECYCLEES
Conception Éco-responsable :
Concevoir des pièces pour une utilisation minimale de matériaux tout en optimisant leur efficacité et leur durabilité est crucial. Les techniques de design pour la durabilité, comme l’allègement et l’intégration de fonctions, permettent de diminuer l’impact environnemental sans compromettre la performance.
Optimisation du Processus de Fabrication :
Mettre en œuvre des pratiques de fabrication économe en énergie, telles que l’utilisation efficace des machines et la réduction des cycles de production, peut considérablement réduire l’empreinte carbone. Des systèmes de moulage par injection plus efficaces et des technologies de refroidissement rapide contribuent également à une consommation énergétique moindre.
Prolongation de la Durée de Vie du Produit :
Créer des pièces plastiques robustes et durables qui nécessitent moins de remplacement aide à diminuer leur impact environnemental sur le long terme. Encourager le recyclage et la réutilisation des produits en fin de vie renforce cette approche.
Recyclage des plastiques en Fin de Vie :
Mettre en place des programmes de collecte et de recyclage des produits en fin de vie assure que les matériaux peuvent être retraités et réutilisés. Éduquer les utilisateurs finaux sur la manière de recycler correctement et fournir des points de collecte accessibles sont des mesures clés.
Utilisation de Bioplastiques :
Là où cela est possible, l’adoption de bioplastiques fabriqués à partir de sources renouvelables peut réduire l’empreinte carbone des pièces moulées. Les bioplastiques peuvent également offrir une alternative compostable au plastique traditionnel dépendant des hydrocarbures.
En mettant en œuvre ces stratégies, les entreprises peuvent non seulement améliorer l’impact carbone de leurs opérations mais aussi prolonger le cycle de vie des produits, contribuant ainsi à un avenir plus durable.
ASSEMBLAGE PLASTIQUE
soudure pièces plastiques
plastiques soudure ultrasons
plastiques soudure vibration
Quels sont les moyens d’assemblage de pièces plastiques ?
L’assemblage de pièces plastiques est une étape essentielle dans de nombreux processus de fabrication, permettant de créer des produits finis à partir de composants individuels. Diverses méthodes peuvent être employées, chacune ayant ses avantages spécifiques en termes de coût, de performance et d’application. Voici quelques moyens courants d’assemblage de pièces plastiques :
Soudure par Ultrason :
Cette technique utilise des vibrations ultrasoniques pour générer de la chaleur par friction au niveau des surfaces de contact des pièces à assembler. Cela provoque la fusion et la soudure du plastique. Elle est rapide et idéale pour les assemblages nécessitant une grande précision et esthétique.
Soudure par Vibration :
Le soudage par vibration implique des mouvements linéaires ou orbitaux entre les deux pièces plastiques pendant qu’une force est appliquée pour les maintenir ensemble. Cette méthode est efficace pour les pièces de grande taille ou complexes.
Soudure à lame chaude :
En utilisant une plaque chauffante pour faire fondre les zones de joint des pièces, cette méthode permet des assemblages solides et hermétiques. Elle est souvent utilisée pour les grandes pièces ou les matériaux thermoplastiques difficiles à souder par d’autres moyens.
Soudure Laser :
Cette méthode utilise un laser focalisé pour fondre les surfaces de jonction des pièces plastiques. Le soudage au laser est précis, propre et adapté aux applications nécessitant des joints très fins.
Collage adhésif :
Différents types d’adhésifs, comme les adhésifs cyanoacrylates, époxy, ou polyuréthanes, peuvent être employés pour assembler des pièces plastiques. Cette méthode est simple, versatile et peut être utilisée pour des matériaux ayant des compositions variées.
Assemblage par Rivetage ou Clips :
L’utilisation de rivets ou de clips en plastique permet un assemblage mécanique sans nécessiter de chaleur ou d’adhésifs. Ces solutions sont rapides à mettre en œuvre et peuvent être réversible selon le design du produit.
Assemblage par Emboîtement / Clips plastiques :
Par emboîtement ou pression, les pièces plastiques peuvent être assemblées en utilisant leurs propres caractéristiques géométriques pour un montage rapide et fiable. Ce type d’assemblage est souvent utilisé pour des produits ayant des tolérances étroites.
En choisissant la méthode d’assemblage la plus appropriée pour vos pièces plastiques, vous pouvez améliorer l’efficacité de votre production, réduire les coûts et assurer la qualité et la durabilité de vos produits finis.
décoration pièces plastiques
tampographie sur plastique
sérigraphie sur plastique
gravure laser sur plastique
Comment décorer une pièce plastique ?
La décoration des pièces plastiques permet non seulement d’améliorer leur aspect esthétique, mais aussi d’ajouter des fonctionnalités supplémentaires telles que la résistance à l’usure ou la conductivité. Voici quelques méthodes courantes pour décorer les pièces plastiques :
Sérigraphie sur plastique :
La sérigraphie est une méthode de décoration utilisée pour imprimer des motifs graphiques sur des surfaces plastiques. Cette technique utilise un écran de soie pour transférer l’encre sur la pièce, permettant des conceptions détaillées et en plusieurs couleurs.
Tampographie :
La tampographie est une technique d’impression par tampon qui permet de transférer de l’encre sur des surfaces courbes ou irrégulières. Elle est idéale pour les petits objets et les détails fins, comme les logos ou les symboles.
Marquage à Chaud :
Le marquage à chaud (ou pressage à chaud) implique l’utilisation de chaleur et de pression pour transférer une feuille métallisée ou colorée sur la pièce plastique. Ce procédé est souvent utilisé pour ajouter des touches métalliques ou des lettres dorées/argentées.
Peinture et Vernissage :
Les pièces plastiques peuvent être peintes à la main ou par pulvérisation pour obtenir la couleur désirée. Un vernis peut également être appliqué pour protéger la surface et ajouter de la brillance. Des peintures spéciales, résistantes aux produits chimiques ou aux UV, peuvent être utilisées pour des applications spécifiques.
Hydrographie :
L’hydrographie, ou impression par immersion, permet de décorer des pièces plastiques en utilisant un film décoratif imprimé flottant sur l’eau. La pièce plongée dans l’eau recouverte de ce film reçoit le motif avec précision, idéal pour les motifs complexes ou continus.
Gravure Laser :
La gravure laser utilise un faisceau laser pour enlever la surface de la pièce plastique dans un motif prédéfini. Cette technique est utilisée pour des marques permanentes et précises, adaptée pour les détails fins comme les codes QR ou les numéros de série.
En utilisant ces différentes techniques de décoration, vous pouvez non seulement améliorer l’attrait visuel de vos produits en plastique, mais aussi ajouter des caractéristiques fonctionnelles qui répondent aux besoins spécifiques de vos clients.
remplacement métal plastique
injection plastique
metal to plastic
métal vers plastique
pièces plastiques structurelles
Remplacement du Métal par le Plastique
Le remplacement des composants métalliques par des pièces en plastique est une tendance croissante dans de nombreuses industries, et ce pour plusieurs raisons. Le plastique offre des avantages significatifs en termes de coût, de poids, et de conception. Voici quelques-uns des principaux avantages et défis associés à cette transition :
Avantages du Plastique par rapport au Métal
Réduction du Poids :
Les plastiques sont généralement beaucoup plus légers que les métaux, ce qui peut être crucial dans des secteurs comme l’automobile ou l’aérospatiale où chaque gramme comptabilise pour les performances et l’efficacité énergétique.
Coût de Production Réduit :
La fabrication de pièces en plastique, en particulier via le moulage par injection, peut-être plus économique que le traitement des métaux. Cela est particulièrement vrai pour la production en grand volume où les coûts de main-d’œuvre et de matériel sont réduits.
Flexibilité de Conception :
Les plastiques offrent une plus grande liberté de conception permettant la création de formes complexes qui seraient difficiles ou coûteuses à produire en métal. Cette flexibilité peut entraîner des conceptions plus innovantes et optimisées.
Résistance à la Corrosion :
Contrairement aux métaux, les plastiques ne rouillent pas et sont résistants à divers produits chimiques, ce qui les rend idéaux pour des applications dans des environnements corrosifs.
Isolation Électrique et Thermique :
Les plastiques agissent comme des isolants naturels, ce qui en fait un matériau de choix pour des applications nécessitant une isolation électrique ou thermique.
Défis à Surmonter
Propriétés Mécaniques :
Les plastiques, même renforcés de fibres, peuvent ne pas offrir la même résistance mécanique que certains métaux. Une évaluation minutieuse des contraintes et des charges est essentielle pour s’assurer que les pièces en plastique répondront aux besoins de l’application.
Tolérances de Fabrication :
Les tolérances de moulage du plastique peuvent être différentes de celles du métal. Il est important de bien comprendre ces différences pour éviter les problèmes de compatibilité lors du remplacement.
Stabilité à la Température :
La performance des plastiques peut être affectée par les variations de température. Alors que certains plastiques haute performance peuvent supporter des températures élevées, la plupart ont des limites de température inférieures à celles des métaux.
Fatigue et Vieillissement :
Les plastiques peuvent se dégrader au fil du temps sous l’effet de la fatigue, des UV, ou des agents chimiques. La sélection du matériau approprié et des additifs stabilisants est cruciale pour prolonger la durée de vie des pièces en plastique.
Conclusion
Le remplacement du métal par le plastique comporte de nombreux avantages et défis. Une analyse approfondie des exigences spécifiques de l’application, ainsi que des propriétés des matériaux, est essentielle pour tirer profit de cette transition avec succès. En combinant les avantages des matériaux plastiques avec les techniques de production modernes, les ingénieurs peuvent souvent obtenir des pièces plus légères, plus économiques, et mieux adaptées aux besoins de leurs projets.
injection bimatière
injection plastique
bimatière
surmoulage plastique
bi injection
Qu’est-ce que l’Injection Bimatière, Quels sont les Avantages ?
L’injection bi matière, également connue sous le nom de surmoulage, est une technique avancée de moulage par injection plastique qui permet l’utilisation de deux matériaux différents pour fabriquer une seule pièce.
Ce procédé implique une première injection de plastique à l’intérieur d’un moule pour former la structure ou le substrat de base de la pièce. Ensuite, un deuxième matériau, souvent de couleur, de texture ou de composition différente, est injecté par-dessus ou autour de la première injection pour compléter la pièce.
Avantages de l’Injection Bi matière
Complexité de Conception :
L’injection bimatière permet de créer des pièces avec des combinaisons de matériaux distinctes qui seraient impossibles ou extrêmement difficiles à obtenir avec des procédés traditionnels. Cela offre des possibilités illimitées pour des conceptions innovantes et fonctionnelles.
Réduction des Assemblages :
Cette méthode permet la production de pièces finies en une seule étape, réduisant ainsi la nécessité d’assemblages supplémentaires. Cela se traduit par des économies de temps et de coûts de production.
Propriétés Améliorées :
Les pièces produites par injection bimatière peuvent combiner les meilleures propriétés de deux matériaux différents, résultant en des produits qui sont plus robustes, résistants aux impacts, aux produits chimiques, ou encore plus esthétiques.
Ergonomie et Esthétique :
L’injection bimatière peut être utilisée pour ajouter des surfaces douces au toucher ou des textures antidérapantes sur des parties spécifiques d’une pièce. Cela améliore non seulement l’apparence esthétique mais aussi le confort et la fonctionnalité du produit final.
Économie de Matériaux :
Ce procédé permet l’utilisation efficace de matériaux coûteux uniquement sur les parties nécessaires, tout en utilisant des matériaux moins coûteux pour la structure principale. Cela peut conduire à des économies significatives de matériaux.
Flexibilité de Production :
L’injection bi matière offre plus de flexibilité dans la production, permettant des changements rapides de configuration et l’intégration de multiples fonctions dans une seule pièce sans besoin de modification majeure du processus de production.
En intégrant l’injection bi matière dans leurs processus, les fabricants peuvent non seulement améliorer la qualité et la fonctionnalité de leurs produits en plastique, mais également réduire les coûts et les délais de production.
injection gaz
injection plastique
injection assistée gaz
injection assistée eau
injection plastique forte épaisseur
Qu’est-ce que l’Injection Assistée Gaz
L’injection assistée par gaz est une technique avancée de moulage par injection où un gaz inerte, typiquement l’azote, est injecté dans le plastique fondu à l’intérieur du moule. Ce processus crée des cavités ou des noyaux creux dans la pièce moulée, permettant ainsi une distribution uniforme du matériau et une meilleure utilisation des ressources. Voici quelques-uns des avantages de l’injection assistée par gaz :
Quels sont les Avantages ?
Réduction du Poids :
En introduisant des cavités creuses dans les pièces moulées, l’injection assistée par gaz permet de réduire considérablement le poids des produits finaux sans compromettre leur intégrité structurelle.
Économie de Matériaux :
Cette méthode utilise moins de matériau plastique sans sacrifier la résistance et la durabilité de la pièce, ce qui se traduit par une réduction des coûts de matériau et une meilleure efficacité de production.
Diminution des Contraintes :
L’injection de gaz aide à réduire les contraintes internes et les marques d’enfoncement sur la surface de la pièce, ce qui améliore la qualité esthétique et la durée de vie des produits.
Meilleur Contrôle de la Qualité :
La technologie permet un contrôle plus précis de l’épaisseur des parois et une meilleure intégrité dimensionnelle des pièces produites, garantissant ainsi des tolérances plus serrées.
Réduction des Temps de Cycle :
Grâce à une distribution plus efficace de la chaleur et à la réduction de la masse de plastique à refroidir, les temps de cycle de production peuvent être significativement réduits, augmentant ainsi la productivité.
Flexibilité de Conception :
L’injection assistée par gaz permet de créer des pièces avec des parois plus épaisses et des changements de section plus lisses, offrant ainsi plus de flexibilité pour des conceptions complexes et innovantes.
Amélioration de la Performance :
Les pièces fabriquées par ce procédé ont une meilleure résistance aux flexions et à l’impact, ce qui les rend appropriées pour des applications nécessitant des performances mécaniques élevées.
En adoptant l’injection assistée par gaz, les fabricants peuvent produire des pièces en plastique plus légères, plus robustes et plus précises tout en optimisant les coûts et les capacités de production.
surmoulage d’inserts
surmoulage
insert molding
surmoulage insert métallique
Qu’est-ce que le Surmoulage d’Inserts
Le surmoulage d’inserts, également connu sous le nom de moulage par insert, est une technique de moulage par injection où des composants préfabriqués, souvent métalliques, sont placés dans le moule avant l’injection du matériau plastique. Ces inserts peuvent inclure des pièces telles que des filetages, des broches, des contacts électriques, ou d’autres éléments fonctionnels qui doivent être intégrés de manière permanente et sécurisée dans la pièce en plastique finale.
Voici quelques-uns des avantages du surmoulage d’inserts :
Renforcement Structurel :
Les inserts métalliques ajoutent une robustesse et une durabilité supplémentaires aux pièces en plastique, permettant de créer des produits capables de résister à des charges plus importantes et à des environnements plus exigeants.
Intégration Fonctionnelle :
Les inserts permettent l’intégration de fonctions supplémentaires directement dans le produit final, telles que des composants électriques ou des mécanismes de fixation, sans besoin d’assemblage ultérieur.
Précision et Répétabilité :
Le surmoulage d’inserts offre une haute précision et répétabilité dans le placement des éléments fonctionnels, garantissant ainsi une qualité constante et une meilleure cohérence entre les pièces produites.
Réduction des Coûts de Production :
En combinant plusieurs étapes de fabrication en un seul processus, le surmoulage d’inserts réduit le besoin de post-traitement et de montage, ce qui peut conduire à des économies significatives en termes de temps et de coûts de main-d’œuvre.
Amélioration de la Fiabilité :
En utilisant le surmoulage d’inserts, les fabricants peuvent éliminer les problèmes potentiels d’alignement et de tolérance associés à l’assemblage manuel, entraînant une meilleure intégrité et fiabilité du produit final.
Flexibilité de Conception :
Cette technique offre une grande flexibilité en termes de conception, permettant de créer des composants complexes avec des caractéristiques spécifiques et un niveau de détail élevé sans compromettre l’efficacité de la production.
En intégrant le surmoulage d’inserts dans leurs processus, les fabricants peuvent produire des pièces en plastique sophistiquées et performantes, tout en réduisant les coûts et en améliorant la fonctionnalité et la qualité des produits finis.
impression 3D vs injection
prototype
inconvénient impression 3D
plastique petite série
Injection Plastique vs Impression 3D
L’injection plastique et l’impression 3D sont deux méthodes distinctes de fabrication, chacune ayant ses propres avantages et inconvénients en fonction de l’application et des besoins de production.
Avantages de l’Injection Plastique
L’injection plastique, comme mentionné précédemment, est extrêmement efficace pour la production de masse. Elle permet de produire des milliers de pièces identiques avec une grande précision et en peu de temps. Cette méthode est particulièrement économique pour la fabrication de grandes quantités de pièces, car le coût par unité diminue considérablement à mesure que le volume de production augmente. De plus, les pièces produites par moulage par injection présentent une haute qualité et une excellente résistance mécanique.
Avantages de l’Impression 3D
D’autre part, l’impression 3D excelle dans la fabrication de prototypes et de petites séries. Elle offre une grande flexibilité de conception et permet de produire des pièces aux formes complexes sans nécessiter de moules coûteux. Cette méthode est idéale pour les itérations de conception rapide, car elle permet de modifier et de produire rapidement de nouvelles versions de pièces. En outre, l’impression 3D utilise souvent moins de matériau et génère moins de déchets que l’injection plastique, car elle ajoute de la matière couche par couche uniquement où cela est nécessaire.
Inconvénients de l’Injection Plastique
Cependant, l’injection plastique comporte des coûts initiaux élevés liés à la conception et à la fabrication des moules, ce qui peut ne pas être justifié pour des productions de faible volume. De plus, les modifications de conception après la fabrication du moule peuvent être coûteuses et complexes.
Inconvénients de l’Impression 3D
Quant à l’impression 3D, bien qu’elle soit bénéfique pour les petites séries et les prototypes, elle est généralement moins rapide et moins rentable pour la production de masse. Les pièces produites par impression 3D peuvent également ne pas toujours atteindre le même niveau de finition et de robustesse que celles fabriquées par injection plastique.
Conclusion
En conclusion, le choix entre l’injection plastique et l’impression 3D dépendra principalement de la nature du projet, du volume de production, de la complexité des pièces et du budget. Pour les productions de masse nécessitant des pièces robustes et finies, l’injection plastique est souvent la meilleure option. En revanche, pour les prototypes, les petites séries et les conceptions complexes, l’impression 3D offre une flexibilité et une économie de matériau considérables.