Construction d’un moule d’injection plastique
Les moules d’injection plastique sont des outils essentiels dans le domaine de la fabrication de pièces en plastique. Utilisés dans une variété d’industries, allant de l’automobile à l’électronique, ces moules permettent de produire des pièces en grande quantité avec une précision et une uniformité remarquables. La méthode d’injection plastique consiste à faire fondre des granulés de plastique pour les injecter ensuite dans un moule, où ils prennent la forme souhaitée en refroidissant et en durcissant.
Ce guide a pour objectif de sensibiliser à la compréhension d’un moule et détailler comment fonctionne un moule d’injection plastique.
L’importance des moules d’injection plastique ne peut être sous-estimée. Ils jouent un rôle crucial dans la chaîne de production, permettant de fabriquer des composants de haute qualité à un coût relativement bas. Cette méthode est particulièrement appréciée pour sa capacité à produire des pièces complexes avec des détails fins, ce qui est souvent difficile à réaliser avec d’autres procédés de fabrication.
Comprendre les différentes parties d’un moule d’injection plastique est crucial pour quiconque impliqué dans la production de pièces en plastique. Une connaissance approfondie des composants du moule permet de mieux anticiper et résoudre les problèmes potentiels, d’optimiser les cycles de production et de garantir la qualité des produits finis. En maîtrisant ces aspects, les fabricants peuvent améliorer leur efficacité, réduire les temps d’arrêt et minimiser les coûts de production.
Les moules d’injection plastique sont au cœur de la fabrication de pièces en plastique. Leur conception et leur fonctionnement influencent directement la qualité, la précision et la rentabilité de la production. Par conséquent, une compréhension approfondie de leurs différentes parties est essentielle pour toute entreprise cherchant à exceller dans ce domaine. Hybster propose ses services de plasturgie à Lille. N’hésitez pas à découvrir nos services.
L’empreinte :
Dans le processus de moulage par injection plastique, l’empreinte (aussi appelé matrice / poinçon) jouent un rôle crucial en déterminant la forme finale de la pièce en plastique. Ces deux composants forment le Plastic mould tool« >moule principal où le plastique fondu est injecté et façonné. La cavité ou matrice représente la partie femelle du moule, tandis que le noyau (ou poinçon) constitue la partie mâle. Ensemble, ils créent l’espace vide qui définira les contours du produit fini.
Le noyau et la cavité sont conçus pour s’emboîter parfaitement, assurant une répartition uniforme de la matière plastique fondue. La cavité est généralement plus profonde et complexe, capturant les détails extérieurs de la pièce, tandis que le noyau, souvent plus simple dans sa structure, forme les surfaces intérieures. Cette interaction entre le noyau et la cavité permet de créer des produits avec des géométries précises et des finitions de haute qualité.
Les matériaux utilisés pour fabriquer le noyau et la cavité sont généralement des aciers spéciaux, choisis pour leur résistance à l’usure et leur capacité à supporter les hautes températures et pressions du processus de moulage. Parmi les matériaux couramment utilisés, on retrouve l’acier inoxydable, l’acier trempé, et parfois des alliages à base de cuivre pour des applications spécifiques nécessitant une dissipation thermique rapide.
La conception des empreintes du moule est une étape critique dans le développement de moules d’injection plastique. Le mouliste doit prendre en compte divers facteurs, tels que le retrait du plastique lors du refroidissement, la facilité de démoulage de la pièce finie, et la minimisation des défauts comme les lignes de soudure et les marques de rétractation. Des logiciels de simulation avancée sont souvent utilisés pour optimiser ces conceptions et garantir une production efficace et de haute qualité. L’étude de l’écoulement du matériau plastique dans l’empreinte s’appelle la rhéologie.
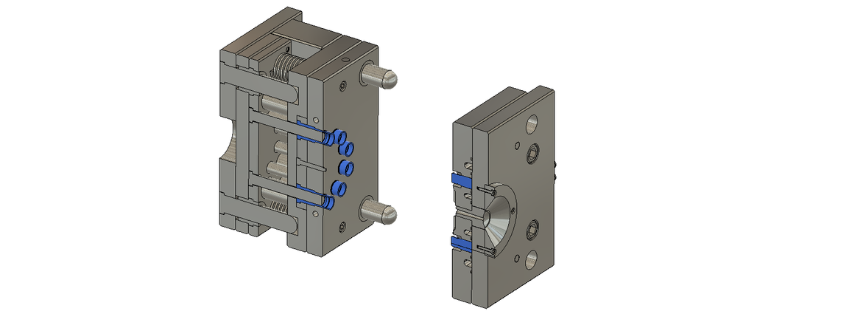
La carcasse du moule
Le châssis du moule, également connu sous le nom de base du moule, constitue la structure fondamentale de tout moule d’injection plastique. Ce composant essentiel est généralement fabriqué à partir de matériaux robustes tels que l’acier ou l’aluminium, sélectionnés pour leur résistance et leur durabilité. Le choix du matériau dépend souvent des spécificités de l’application, incluant la nature du polymère utilisé et les exigences de production.
La fonction principale du châssis du moule est de maintenir l’intégrité structurelle de l’ensemble du moule. Il assure la stabilité nécessaire pour que toutes les autres parties du moule fonctionnent correctement. En d’autres termes, il sert de squelette rigide, supportant les composants mobiles et fixes, tels que les plaques de cavité et de noyau, ainsi que les systèmes de refroidissement, d’éjection, et d’alimentation en matière plastique.
Le châssis du moule doit également être conçu pour résister à des pressions élevées et à des cycles répétés de chauffage et de refroidissement. Cela garantit non seulement la longévité du moule mais aussi la qualité constante des pièces moulées. De plus, les tolérances dimensionnelles strictes du châssis permettent un alignement précis des autres composants, minimisant les défauts de production et maximisant l’efficacité.
Il existe différentes variations de châssis de moule adaptées à diverses applications spécifiques. Par exemple, pour des productions de haute précision, on peut utiliser des châssis en acier trempé, tandis que pour des applications moins exigeantes, des châssis en aluminium peuvent suffire. D’autres variations incluent des châssis modulaires, qui permettent des ajustements rapides et une flexibilité accrue dans les paramètres de production. En somme, le choix du châssis du moule dépend largement des exigences de l’application, des matériaux utilisés, et des conditions de production.
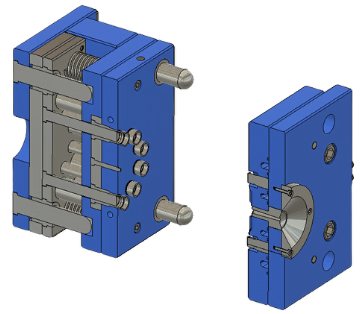
Le système de canaux d’alimentation
Dans le processus de moulage par injection plastique, le système de canaux d’alimentation joue un rôle crucial. Ce système comprend plusieurs composants essentiels : les canaux d’alimentation et les seuils d’injection plastique . Chacun de ces éléments contribue à l’acheminement précis et efficace du plastique fondu depuis la machine d’injection jusqu’aux cavités du moule.
Les canaux de coulée, également appelés systèmes de distribution, sont les premières voies par lesquelles le plastique fondu passe après avoir quitté la buse de la machine d’injection. Ces canaux peuvent être conçus de différentes manières, incluant des configurations en étoile, en arbre ou en réseau, selon les besoins spécifiques du produit à fabriquer. Une bonne conception des canaux de coulée est essentielle pour garantir une distribution homogène du matériau et minimiser les pertes de matière.
Les buses jouent un rôle intermédiaire en reliant les canaux de coulée aux portes d’injection. Elles doivent être conçues pour maintenir la température du plastique fondu, éviter les fuites et faciliter un flux continu de matière. Un design optimal des buses permet de réduire la pression nécessaire pour l’injection et améliore ainsi l’efficacité énergétique du processus.
Enfin, les seuils d’injection sont les points d’entrée du plastique fondu dans les cavités du moule. Il existe plusieurs types de portes, comme les portes à languette, à tunnel ou à bouton, chacune ayant des propriétés spécifiques en termes de contrôle du flux, de facilité de retrait et de qualité de la pièce moulée. La position et la taille des portes sont également déterminantes pour éviter les défauts de moulage tels que les marques de soudure ou les bulles d’air.
L’importance d’un design efficace du système de canaux d’alimentation ne peut être sous-estimée. Un système bien conçu non seulement optimise le processus de moulage mais également réduit les déchets de matière et les coûts de production. En assurant une distribution uniforme du plastique fondu et en minimisant les pertes thermiques, il contribue à la production de pièces de haute qualité, tout en améliorant la rentabilité et la durabilité des opérations de moulage par injection plastique.
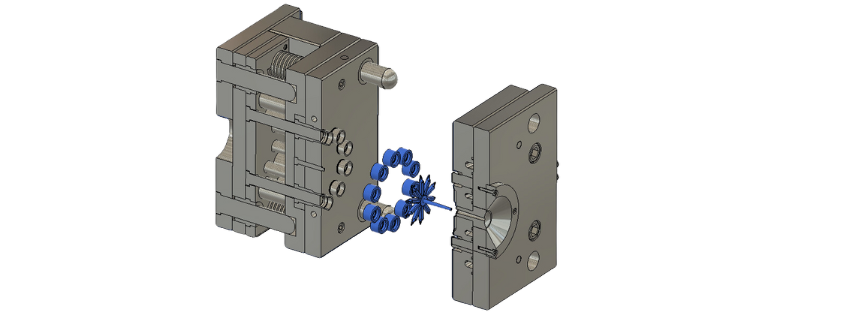
Les éjecteurs
Les éjecteurs jouent un rôle crucial dans le procédé de moulage par plastic injection moulding. Une fois que la pièce moulée a refroidi et s’est solidifiée, les éjecteurs interviennent pour expulser la pièce du moule. Il existe plusieurs types d’éjecteurs, chacun ayant des caractéristiques spécifiques pour répondre aux besoins particuliers du processus de moulage.
Les éjecteurs à tiges sont les plus couramment utilisés. Ils consistent en une série de tiges métalliques qui poussent la pièce moulée hors de la cavité du moule. Les éjecteurs à lames, quant à eux, sont plus fins et sont utilisés pour des pièces nécessitant une éjection plus délicate. Enfin, les plaques éjectrices sont des plaques métalliques qui poussent la pièce en exerçant une force uniforme sur une plus grande surface.
Le fonctionnement des éjecteurs est relativement simple. Lorsque le cycle de moulage est complété, le moule s’ouvre, et le mécanisme d’éjection est activé. Les tiges, lames ou plaques éjectrices poussent alors la pièce hors du moule. Cependant, la conception et l’intégration des éjecteurs dans le moule doivent être précises pour assurer un fonctionnement fluide et éviter d’endommager les pièces moulées.
Un système d’éjection bien conçu est essentiel pour plusieurs raisons. Premièrement, il minimise les risques de dommages aux pièces moulées, ce qui est crucial pour maintenir la qualité du produit. Deuxièmement, il assure une production continue en réduisant les temps d’arrêt nécessaires pour retirer les pièces manuellement. Enfin, un bon système d’éjection permet d’optimiser l’efficacité globale du processus de moulage, réduisant ainsi les coûts de production et augmentant la productivité.
En conclusion, les éjecteurs sont une composante indispensable des moules d’injection plastique. Leur conception et leur intégration doivent être soigneusement planifiées pour garantir une éjection efficace et sans dommage des pièces moulées, contribuant ainsi au succès global du processus de moulage.
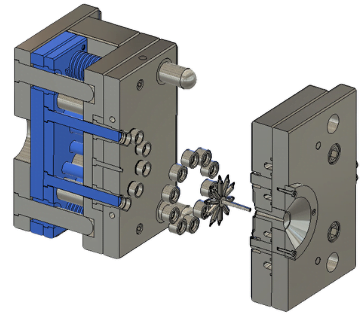
Les systèmes de refroidissement
Les systèmes de refroidissement des moules d’injection plastique jouent un rôle crucial dans le contrôle de la température du moule, garantissant ainsi une solidification rapide et uniforme du plastique injecté. Un refroidissement efficace est essentiel non seulement pour améliorer la qualité des pièces produites, mais aussi pour réduire les cycles de production, optimisant ainsi l’efficacité globale du processus de moulage.
Il existe plusieurs types de circuits de refroidissement utilisés dans les moules d’injection plastique. Les circuits de refroidissement conventionnels utilisent des canaux linéaires ou hélicoïdaux percés dans le moule, à travers lesquels circule un fluide de refroidissement, généralement de l’eau. Ces circuits peuvent être simples ou multiples, selon la complexité de la pièce et les exigences de refroidissement.
En plus des circuits conventionnels, des systèmes de refroidissement conformes ont été développés pour mieux s’adapter à la géométrie complexe des pièces moulées. Ces systèmes utilisent des canaux de refroidissement qui suivent de près les contours de la cavité du moule, permettant un refroidissement plus uniforme et efficace. L’impression 3D et la fabrication additive sont souvent utilisées pour créer ces canaux conformes, offrant ainsi des possibilités de conception plus flexibles.
Les matériaux utilisés pour les systèmes de refroidissement des moules sont également un facteur clé. L’acier inoxydable est couramment utilisé en raison de sa résistance à la corrosion et de sa durabilité. Cependant, pour des applications nécessitant une conductivité thermique plus élevée, des alliages de cuivre peuvent être utilisés, bien qu’ils soient moins résistants à l’usure. Le choix du matériau dépendra des exigences spécifiques de l’application, incluant la durée de vie du moule et les paramètres de production.
Un système de refroidissement bien conçu peut significativement améliorer la qualité des pièces moulées en minimisant les déformations et en assurant une solidification uniforme. De plus, en optimisant le refroidissement, les cycles de production peuvent être réduits, ce qui se traduit par une augmentation de la productivité et une réduction des coûts de fabrication. En somme, les systèmes de refroidissement sont un élément essentiel pour garantir l’efficacité et la qualité des processus de moulage par injection plastique.
Retrouvez notre guide de l’injection plastique, parcourant les matières et les conseils de conception de pièces plastique.